end-to-end gas detection solution
Autonomous inspection for oil & gas

Minimize refinery downtime with autonomous inspections
A U.S. downstream refinery sees $2M ROI with autonomous inspections minimizing downtime.
Companies reduce O&M costs and prevent serious failures with daily, remote inspections. Autonomous drones and robots powered by Percepto Autonomous Inspection and Monitoring (AIM) leverage AI-powered algorithms to detect leaks, faults and failures right away – minimizing downtime every day.
Spotlight on autonomous gas leak detection
The only drone-in-a-box with an integrated OGI camera.
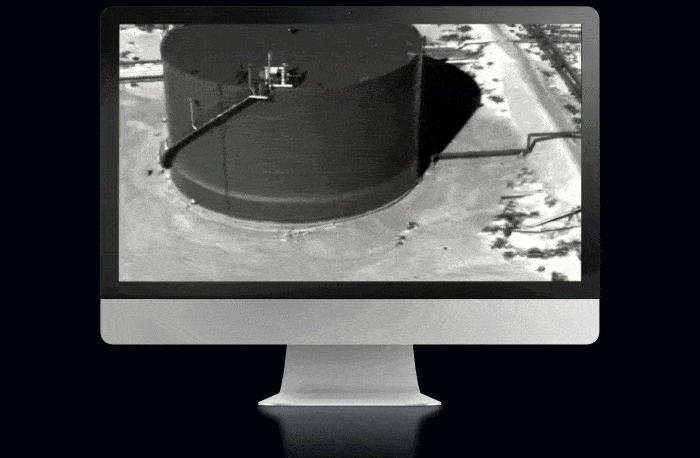
ROI at a glance
Automated inspections at a U.S. refinery
Top use cases at refineries:
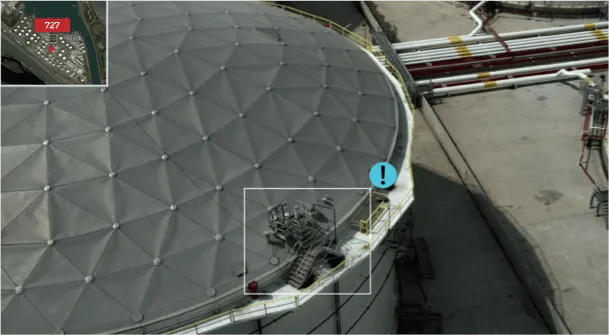
Oil tank inspection
Conduct pre-scheduled automatic tank inspection missions scanning for environmental hazards, structural damage and other faults.
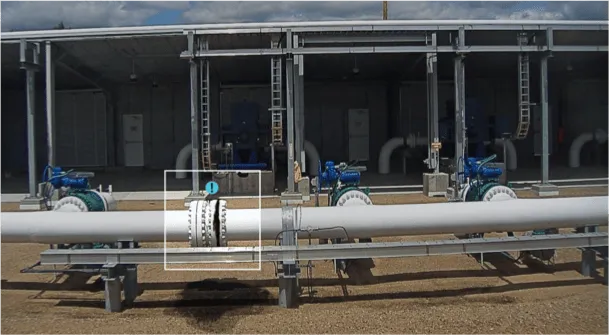
Leak detection
Never miss a leak with frequent, autonomous inspections and Percepto’s change detection framework.
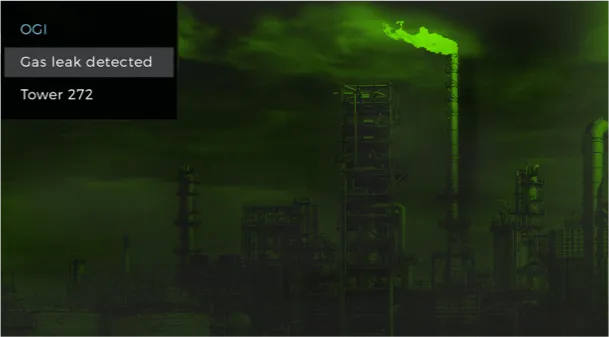
Gas emission detection
The Air Max is the only drone-in-a-box with OGI camera, capable of detecting gas emissions.
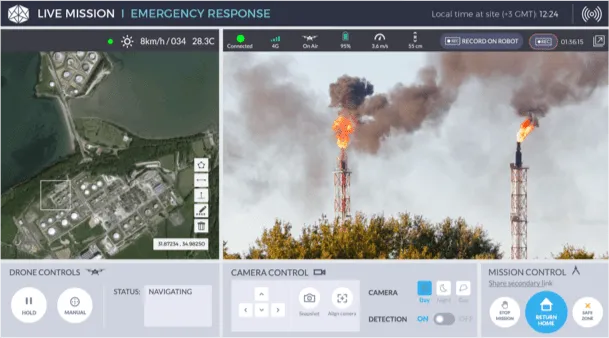
Emergency response
On-site industrial drones or robots are deployed without any human intervention in the event of a fire, leak or other emergency.
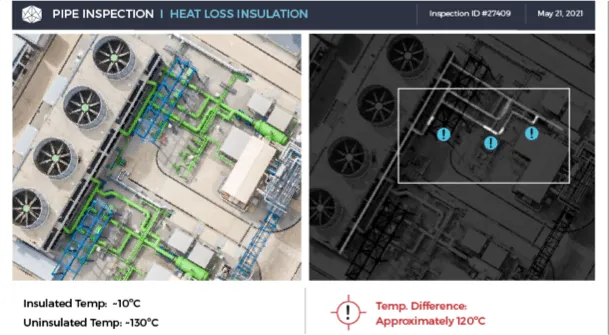
Pipe inspection
Pipe inspections with RGB and thermal cameras detect structural defects as well as insulation faults and environmental breeches.
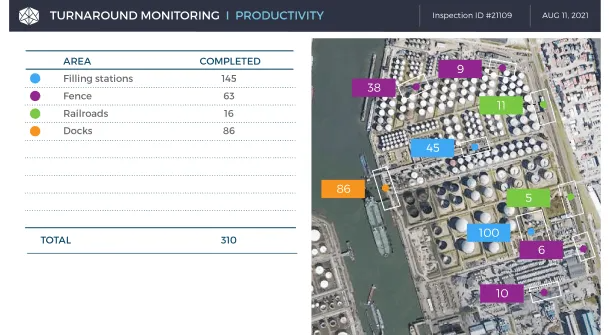
Turnaround monitoring
Monitoring actual turnaround progress and safety on a daily and hourly basis for accurate up-to-date monitoring.
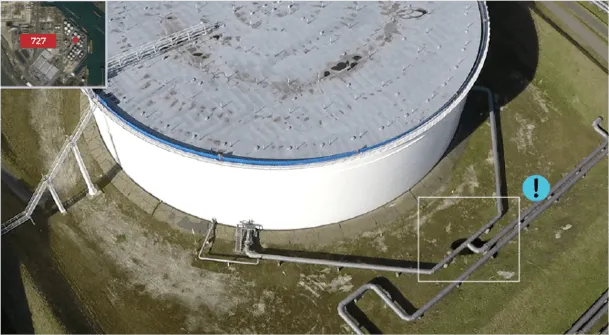
Operations & maintenance
Regularly monitor for “housekeeping” tasks – and never miss an open hatch, equipment left out or other hazards.
Our technology
Percepto’s solution for oil & gas consists of autonomous robots managed by Percepto AIM deployed across a site, with a sophisticated cloud backend for AI-powered site inspections, monitoring, surveillance, and visual data collection & management.
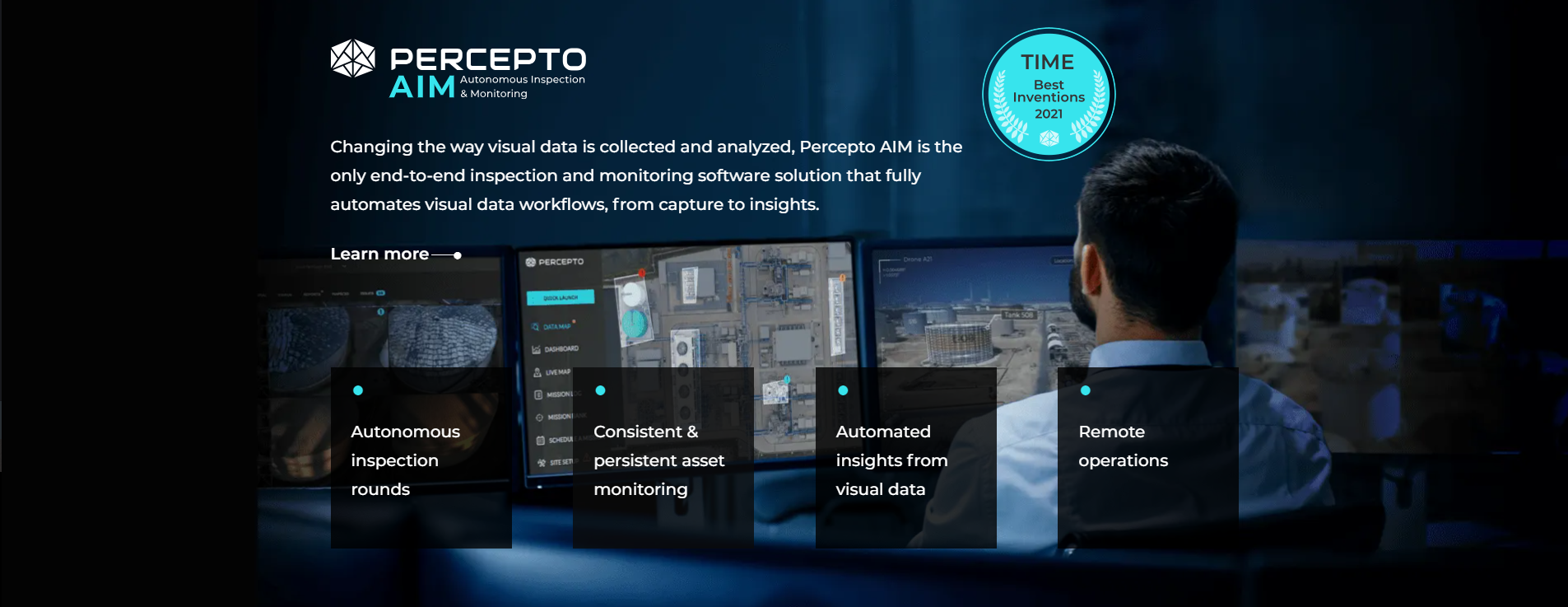
Percepto enables refineries to:

Prevent downtime
Detect corrosion, leaks, poor insulation and more as soon as they happen – preventing faults from turning into shutdowns.

Optimize turnarounds
Effectively meet deadlines and ensure safety with 24/7 autonomous monitoring and AI.

Boost productivity
Free up valuable employee time & increases facility production with autonomous refinery inspections.

Increase safety
Detect spills, leaks & other hazards protecting your employees, the environment and the surrounding community.
FAQs Autonomous inspections at refineries
At any refineries, inspections are conducted to evaluate the health of all site assets. Refinery inspections are critical to meet safety and environmental standards, as well as ensure optimal facility production. Inspectors generally look for corrosion, leaks, structural damage or other hazards or faults.
Drones have proven to be a safer and more efficient alternative to manual inspections. Employees can leverage the quick and low-risk ability of drones to inspect assets such as tanks, pipes and flares.
A shutdown is any disruption of production, usually caused by an unplanned failure. A turnaround is a planned pause in production to evaluate facility health and perform major maintenance.
Most refineries conduct turnarounds every three or four years. During a turnaround, refineries have the opportunity to make repairs or replacements to any assets to ensure optimal facility performance until the next scheduled turnaround.
A variety of technologies and sensors are used to inspect oil and gas pipeline inspections, backed up by regular visual inspections. Visual inspections by drones or ground robots inspect for leaks, insulation thinning, corrosion, and blockage in the right of way.
Several technologies are used to perform non-destructive testing (NDT) of storage tanks – including laser scanners and magnetic flux leakage. Visual inspections are also required to confirm structural integrity of the tank and roof, inspecting for any visible leaks, corrosion or damage.
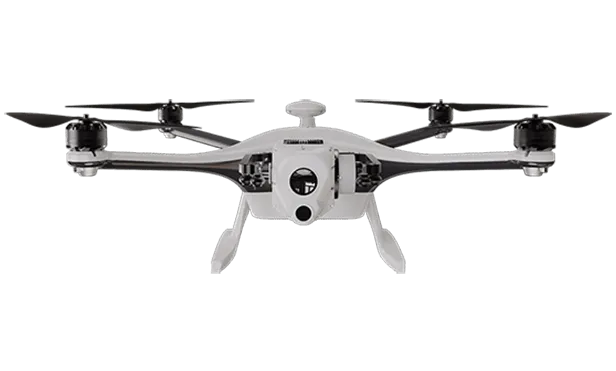